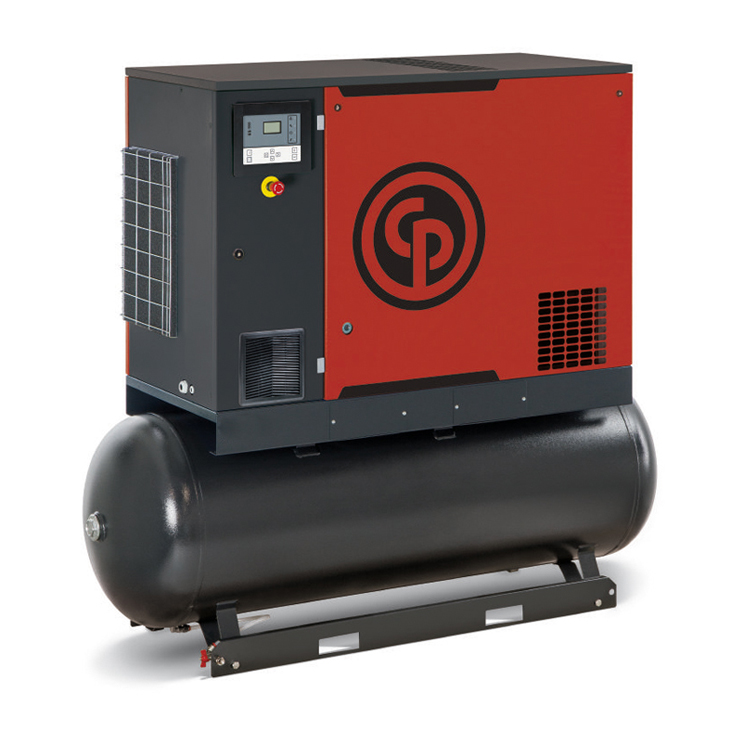
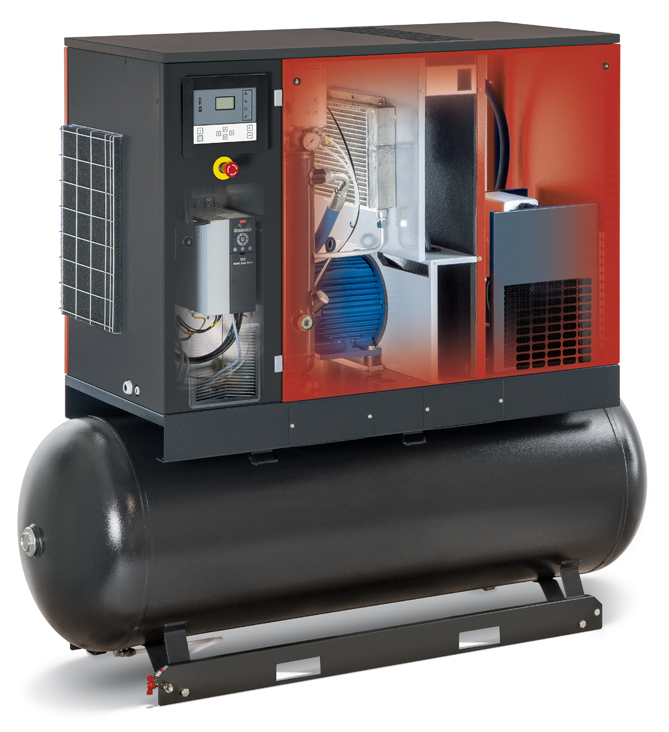
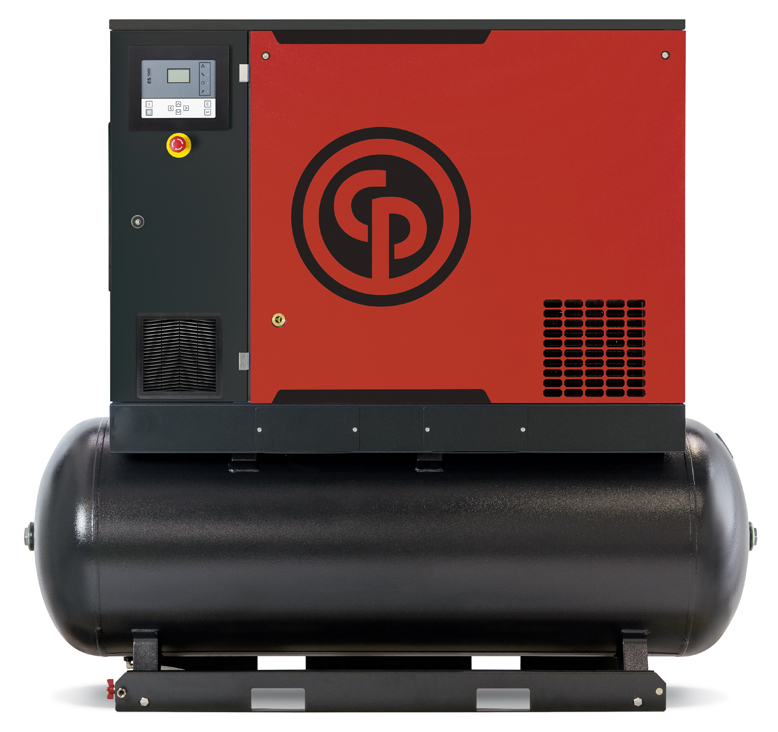
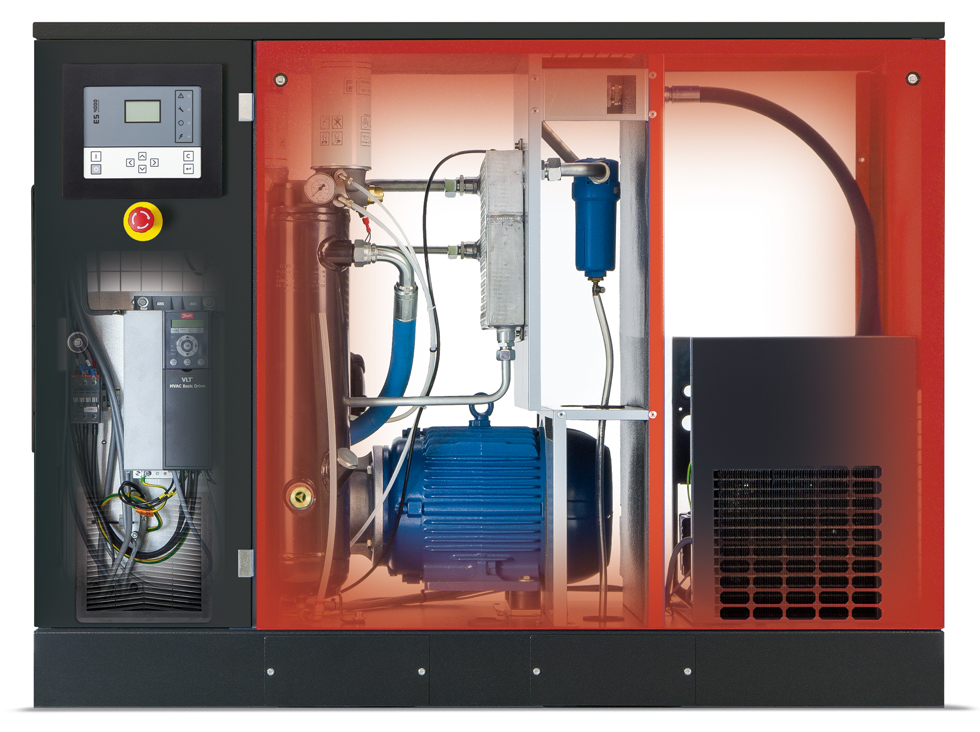
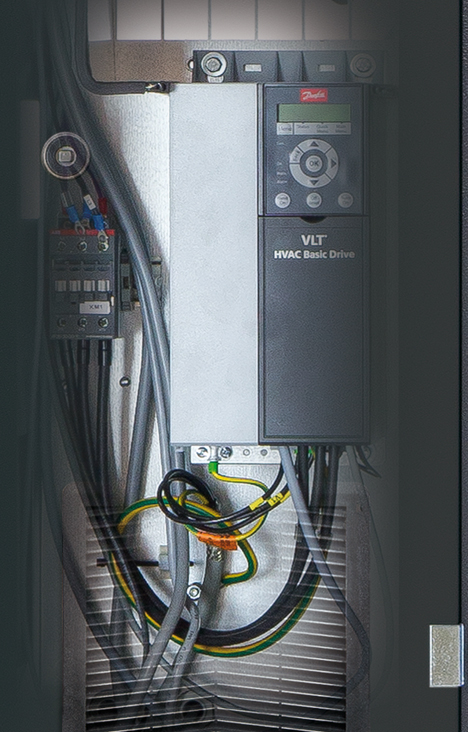
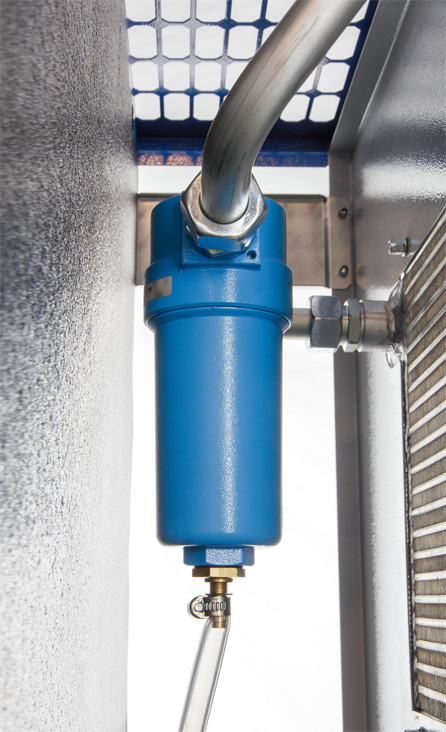
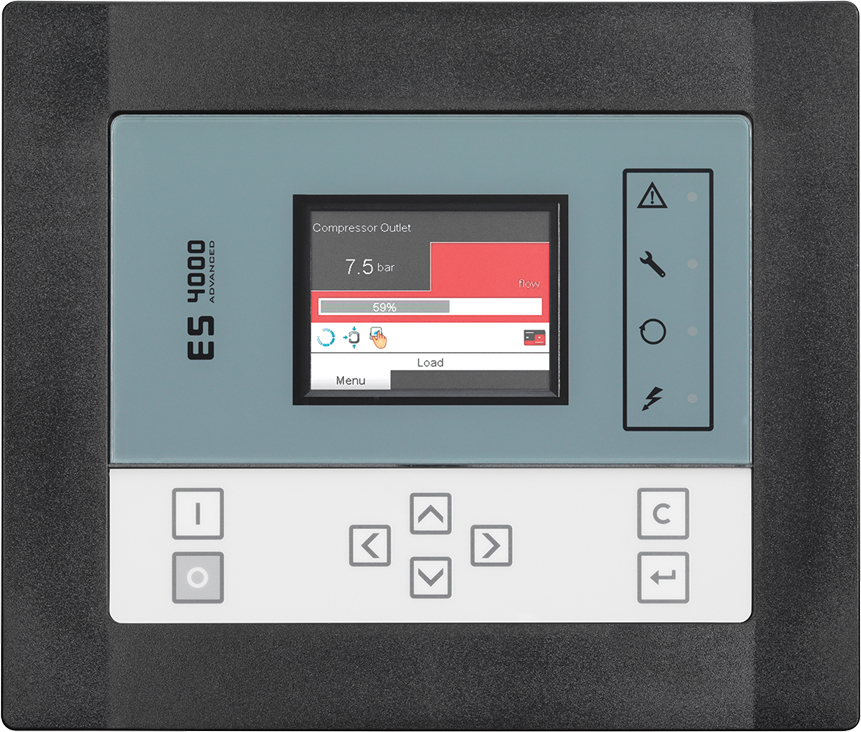
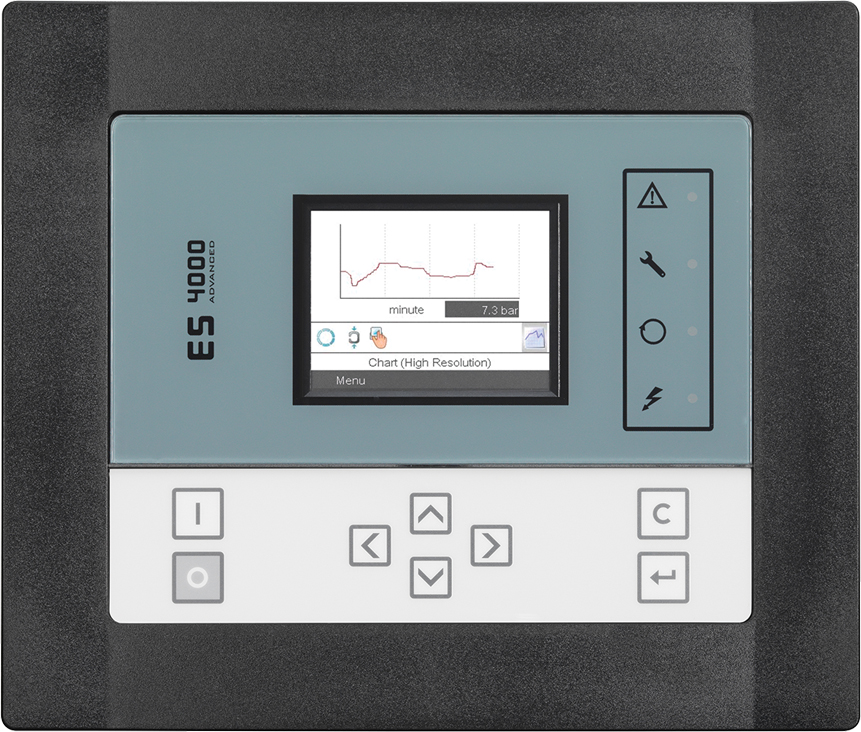
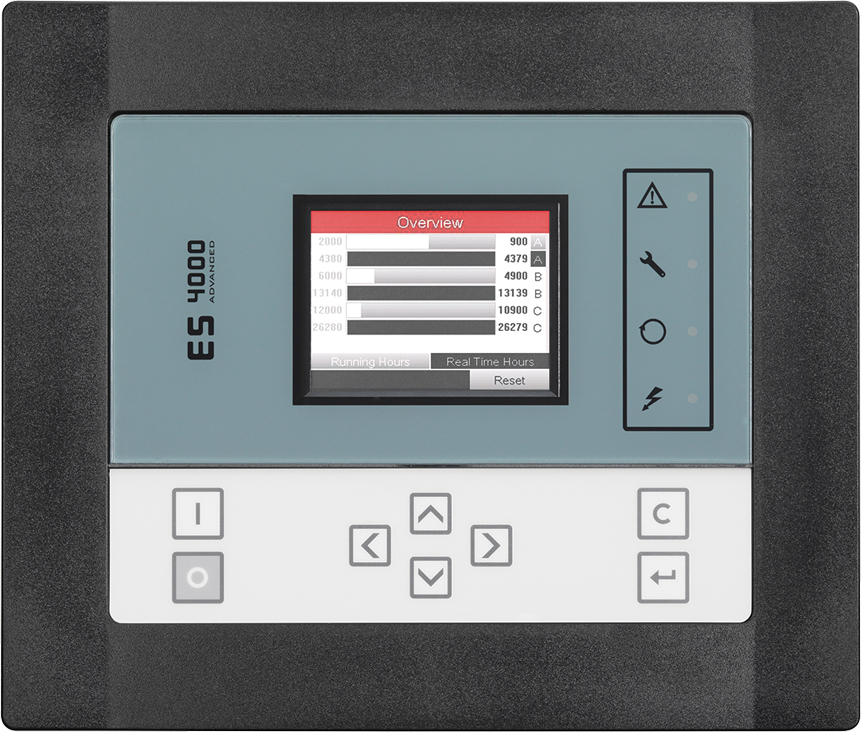
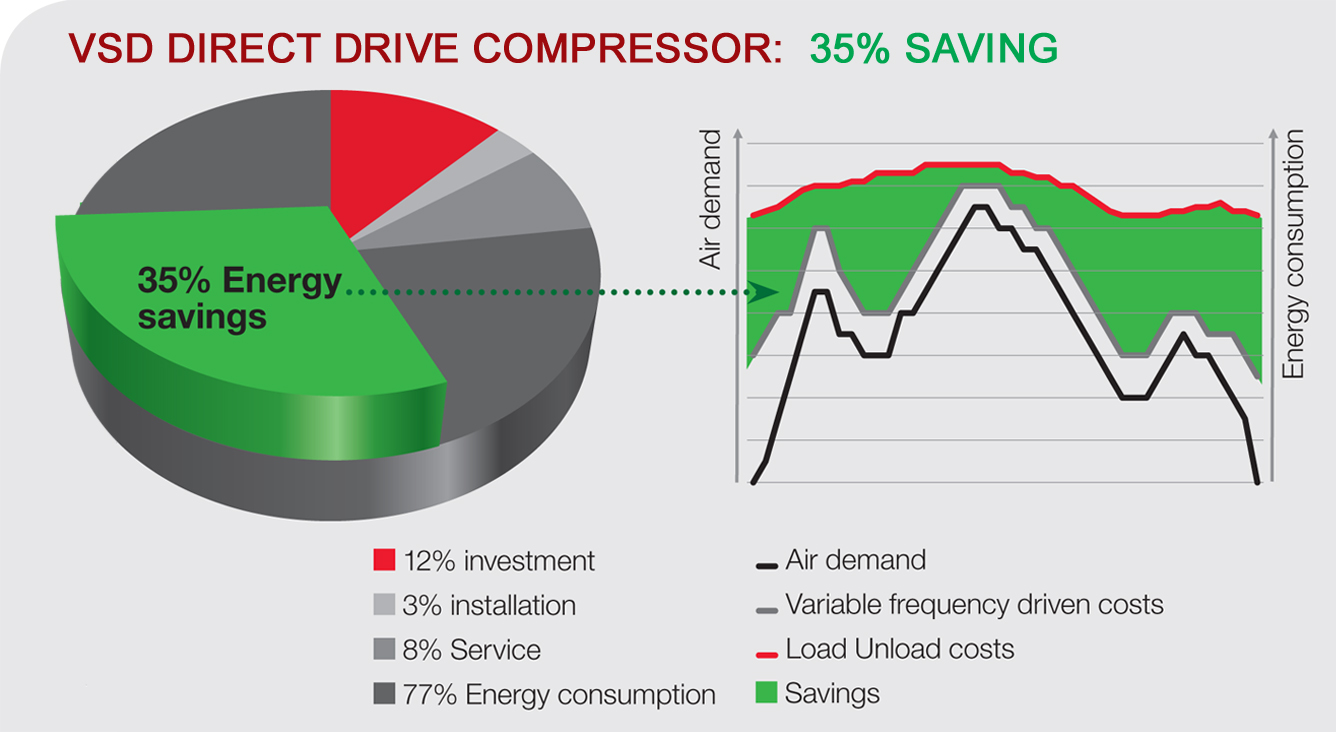
Chicago Pneumatic CPVSd 10 Oil Injected VSD Driven Screw Compressor with 270 L Receiver + Dryer
- Overview
- Specifications
Advanced VSD direct drive in a perfect all-in-one solution
CPVSd 10 is a super smart all-in-one solution that supports your business growth. Combining an intelligent Variable Speed Drive (VSD) with an advanced direct driven transmission together with a high-frequency motor, the CPVSd 10 is the most recommended compressed air solution for future-proof businesses. Up to 35% of energy saving can be achieved by this clever combination. High-quality elements are also used in making the CPVSd 10 a perfect compressor for you.
in the workshop, without disturbing your working environment. Base mounted or tank mounted, with or without dryer, the CPM is a complete solution for your business.
Benefits of Variable Speed Drive
- High energy efficiency with an intelligent inverter and sensors
- Smooth start - no peak current penalties on mechanical parts at start-ups (prolong components' life)
- Reduced system pressure = Reduced energy consumption
- Reduced system pressure = Minimised air leakages
- Complete with 270L receiver and dryer
- Highly efficient C55 Star Air-end
- VSD + Direct drive - High energy efficiency
- Low costs of ownership
- Quiet: 62 dB(A)
- ES4000 ADVANCED graphic controller
Key benefits
- Highly efficient element ensures low energy consumption and long term performance
- Highly efficient belt transmission reducing energy consumption
- Direct driven transmission for further energy saving (CPVSd)
- Protects your air network against rust and corrosion thanks to integrated solutions (dryer, air filter,…
- Inverter technology perfectly matching the air flow with the air demand saving energy costs up to 30%
- User-friendly controller for full control
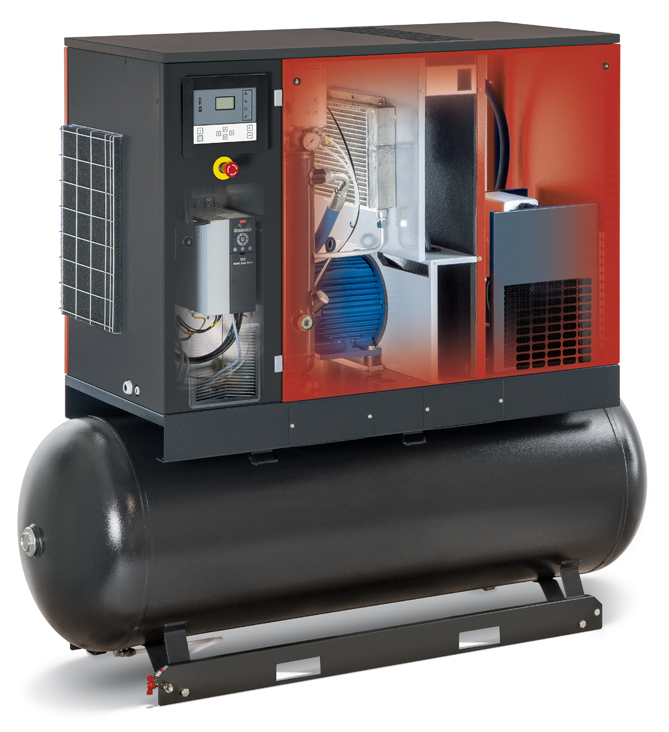
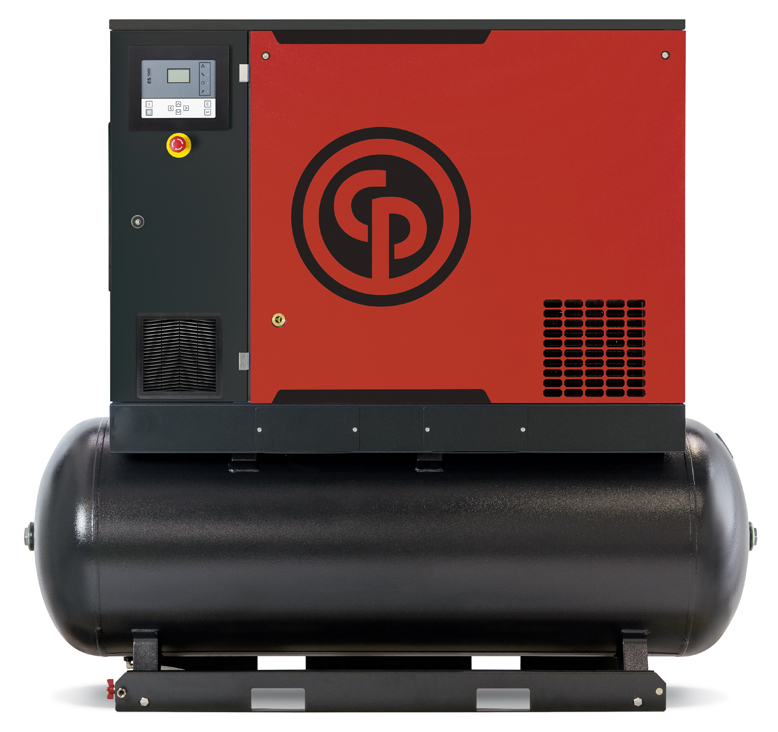
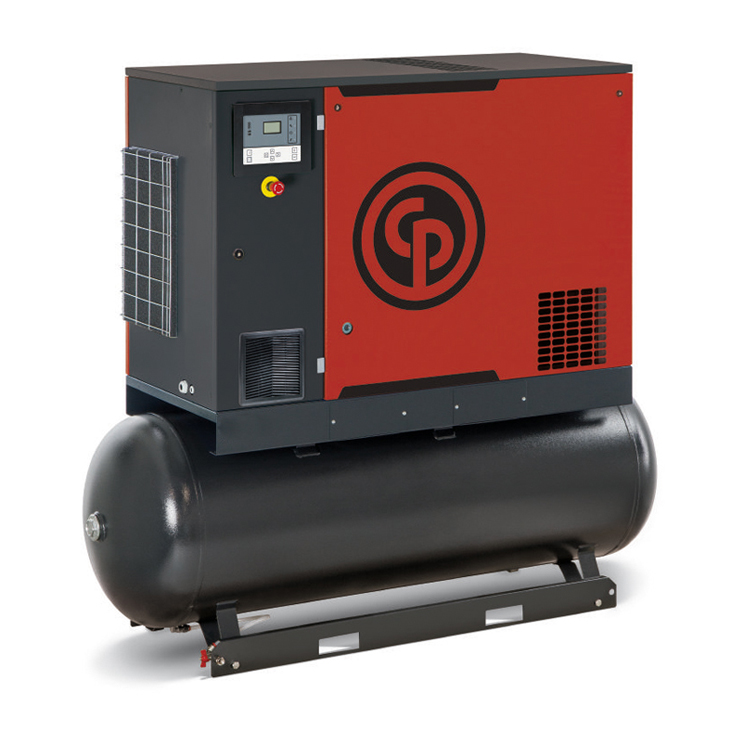
Features
Cost energy reduction and sustainability
Up to 35% of energy savings and an average cut of 25% in the compressor lifecycle cost thanks to IE3 motors or Variable Speed technology, combined with the direct driven transmission design. Optimal efficiency, lubrication and cooling and long service intervals
Customisable with wide range of options
This rotary screw compressor range is available in Variable Speed direct –driven and Fixed speed gear driven versions. Customable options include energy recovery to reduce energy bill and canopy heaters for low temperature installation
Simple installation
Compact and all-in-one system, thanks to the oversized integrated dryers. No special foundation needed
Built to last
ES-4000
Easy access for servicing
All service components are located at the front of the machine for top accessibility.
VSD Energy Savings
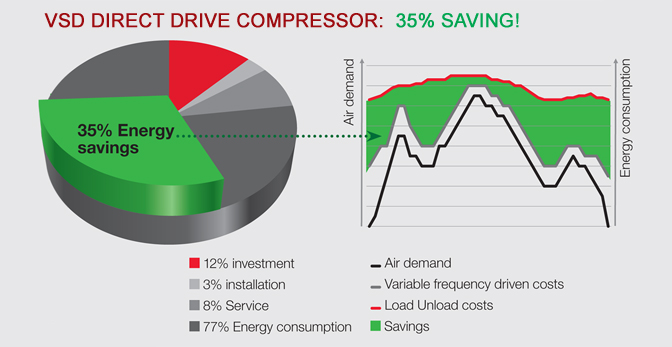
Energy Efficiency
Variable Speed Drive (VSD) compressors can save up to 35% of system energy costs.
More than 80% of a compressor’s lifecycle cost comes from the consumption of energy. Therefore we focus on reducing your energy bill by adapting your compressors’ output with the demanded air input.
How it works
Operations have a fluctuating demand for air, so our VSDÂ technology for compressors makes sure that you and your business get the required air at the required time.
This makes sure that your compressor is not using more energy than needed, effectively decreasing your energy consumption, and increasing your energy efficiency.Â
More than 80% of a compressor’s lifecycle cost comes from the consumption of energy.
Therefore we focus on reducing your energy bill  by adapting your compressors’ output with the demanded air input.
On average we save your company 35% of the energy cost usually related to compressor costs. This gives you a competitive advantage.
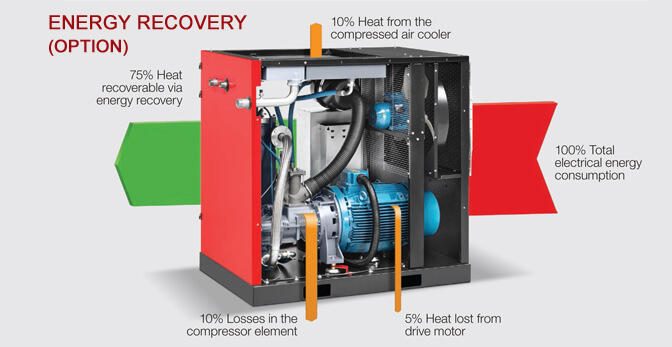
Energy Recovery
The energy recovery option can capture heat and recover up to 75% of energy loss.When looking at the typical carbon footprint of an air compressor - from the design phase right through to the equipment’s recycling - the energy consumed in its use accounts for 99% of CO2 emissions.
As energy consumption also typically represents over 80% of a compressor’s lifecycle cost, energy savings in compressed air systems will have a significant impact towards preserving not only the environment but also your bottom line.
While compressed air systems in general account for about 10% of total industrial electricity consumption, this can amount to as much as 40% of the electricity bill for certain plants.
How does compressor heat recovery work?
Up to 94% of the electrical energy is converted into compression heat. Without energy recovery, this heat is lost into the atmosphere via the cooling system and radiation.
You can use hot water recovered from the compressed air system for sanitary purposes and space heating. But it is particularly suitable for process applications. Using the hot water as boiler pre-feed or directly in processes requiring 70 to 90°C can save you costly energy sources such as natural gas and heating oil.